Permanent Electrical Conductivity with Hubron’s Conductive Compounds and Composites
Conductive polymers and plastics are increasingly desired for a growing number of sophisticated end-uses.
Most plastics are naturally non-conductive, hence their wide use as electrical insulators. Because of their ease of fabrication, chemical inertness and low density, polymers are highly desirable materials as replacements to conventional materials. When some transfer of electrical charge is needed, modifications to the polymer must be made to increase conductivity. This has resulted in plastics being formulated for use in four distinct application categories of increasing conductivity:
01
Insulating (e.g. wire coating)
02
Dissipative (“anti-static” polymers)
03
Conductive (materials capable of conducting modest amounts of electrical current)
04
Highly Conductive or Shielding (materials capable of conducting significant amounts of electrical current)
The tendency of materials to conduct electricity is generally expressed in terms of surface resistivity Ohms per square (Ω2) – i.e. how resistant they are to the transfer of electrons.
Generally thermoplastic polymers have a surface resistivity of 1012 to 1016 Ω2 which characterizes low transfer of electrons making them effective insulators. To overcome this limitation, electrically conductive additives are added to the polymer compound.
The secret behind the best selection of compound/ concentrate lies in three important factors:
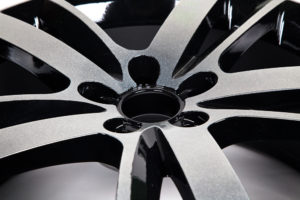
Selecting the optimal carbon particulate type for the purpose
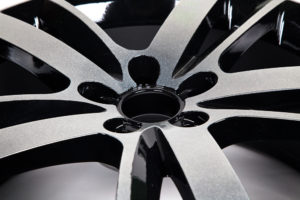
Formulating the compound/ concentrate to get the optimal balance of appearance, physical, chemical and electrical properties
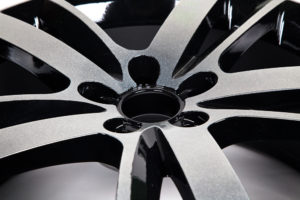
Optimising the melt processing and fabrication
Electrical Conductivity of Carbon Particles in Polymer Compounds
After exceeding a certain loading level of conductive particles, a polymer compound changes the electrically insulating base polymer into electrically conductive plastic. The decrease in electrical surface resistivity is due to the increased amount of particles and can be described using a percolation model. The percolation behaviour depends on aspect ratio of the particle, the particle size and its density and the chemical structure.
The percolation curve illustrates the relationship between the quantity by weight of added conductive additive and the achieved electrical resistivity. There is a narrow threshold in which the electrical resistivity dramatically drops. After this threshold level, increasing the amount of conductive additive will only marginally improve the electrical properties.
Hubron Conductive Compound PDF
Conductive Concentrate Grades PDF
With an extensive knowledge of dispersion of carbon nano-particles into polymers, Hubron has developed a range of conductive compounds and concentrates based on carbon particulates (high structure carbon black, graphite’s, grapheme’s and carbon nanotubes) incorporated into specially selected polymer grades to offer the most reliable and cost-efficient choice for producing electrically conductive plastic compounds. We are also able to develop a grade suitable for you.